Introduction
Operation management is a multidimensional term and people often misunderstood it. Mostly, it’s because the operational functions of various businesses are different, and they operate differently. Today, we’ll discuss what is operation management, its various roles, and the planning operation system.
What is Operation Management?
The focus of operation management is to manage various processes in order to manufacture and distribute the product/service while keeping in mind efficiency and effectiveness. It often comprises analysis, measurement, and evaluation of internal processes of the company.
The nature of how operation management functions within the company are often reliant on the product/service of the company like general service, construction, mining, and agriculture, etc.
Explanation
Operation management is the process of using a company’s resources like raw material, technology, material, labor, and equipment in order to produce the product and to meet the needs and wants of customers.
It deals with different strategic issues like IT networks, implementation structure, methods of project management, and size of manufacturing plants. Some of the other operational issues are maintenance policies, material handling, quality control, raw material acquisition, levels of work in progress, and inventory management levels.
Products & Services
A product is a physical or tangible thing that the company offers to the customers like pair of pants, shoes, a table, wood, paint, etc. People exchange products for a one-time value. Whereas the service is a non-physical or intangible offer, and its utility lasts for a long time.
Roles in Operation Management
Some of the main roles and titles in operation management are as follows;
Chief Operations Officer
COO (chief operating officer) is the highest executive position in the company. Its role is to manage the daily operations of the company and report it to the top management of the company as CEO. However, the COO is the second authority figure in the company after the CEO.
Operations Manager
The role of operation managers is to supervise functions like production, job design, operation staffing, supply chain management, inventory, and delivery. Its job is to manage the main operation of the company that could have a massive strategic impact on the company. However, other roles and responsibilities rely on the nature of the product/service that the company is producing.
Operation System
Before discussing the operation system, it’s important to be familiar with the concept of the system. The system is a collection of various parts combined in a unique way in order to achieve certain goals. A system receives many inputs and then goes through different processes before delivering the final product.
Operations System
The management of the system is the main activity of operation management. The operation manager has to make sure that various parts of the operating system work efficiently and effectively to deliver the final products/services for customers. Some of the main activities in the operating system are as follows;
- Input: it includes the company’s strategic priorities, feedback of customers, technology, facilities, equipment, funding, various practices, and expertise.
- Process: it comprises various planning elements like quality control, inventory, job, production facilities, design of product/service, productivity management, and capacity planning
- Output: delivering a quality product/service
- Outcome: satisfying the needs and wants of customers
You should ask customers for their feedback and use it as input and implement it in the process in the development of the product/service. The operating system works in the form of a recurring loop and produces output and outcomes.
Alignment with Strategic Planning
If you want the system to work efficiently and effectively, then you have to combine the operating system with the company’s goals and mission statement. There should be an alignment with the strategic planning of the company and its operating system.
Planning of Operation System
Some of the main elements in the planning of the operating system are as follows;
Product/Service Planning
When it comes to the planning of the product/service, then you have to conduct market research in order to know certain details like;
- Finding needs and wants of potential customers and looking for ways how to meet them with your offer
- Planning that how you’re going to offer the new product/service to target customer market
- Recognizing your collaborators and competitors in the market
- Setting the best price for your product/service
- Advertising and promoting your offer among your target audience
You can further add specific information like management, facilities, employees, product/service, and add this information in the company’s business plan.
Capacity Planning
Capacity planning discusses how much product/service you have to produce and how often you need to manufacture them. It comprises of forecasting and predicting the market demands. Some of the main tools that you can use are as follows;
- Forecasting total market demand
- Selecting the right prediction technique
- Demand forecasting and how it guides your business
Planning allows you to make an estimate of the product/service that you need to produce like technology, equipment, type of material, skill and expertise, etc.
Layout/Facilities Planning
Facilitating effective and efficient production activities and the maintenance process are the main activities in operation management.
Work/Job Design
Job and work design are one of the main functions of HRM. Its goal is to arrange the workplace in such a way in order to reduce job dissatisfaction and employee alienation. However, it often results when the workplace becomes mechanical due to recurring tasks.
Work Flow Management
Workflow management is the process of creating and optimizing the work path in such a way that would finish the work on time. Some of the main activities in workflow management are recognizing improvement areas, automating the process, finding redundant tasks, and mapping out the workflow.
Planning Inventory/Operations/Quality Control
Production & Scheduling
Production Planning
The production planning is a part of the operating system process where you convert input material into a product. Some of the things that you should keep in mind are as follows;
- Any available technology that could finish the task quickly
- Best way to produce the product by various experts
- Anyone would buy the components of the product
- Elements and parts you need to develop the product/service
- Cost of producing the product/service
- Forecasted demand for your product
Scheduling
Scheduling is a critical activity in the operating system that makes sure efficiency and effectiveness by developing coordination among various activities like production, people, and equipment optimization, monitoring, and timing to organize activities.
Inventory & Supply Chain Management
Supply Chain Management
The supply chain is the process of organizing various supply chain activities in order to gain a competitive edge and optimize customer value. It requires the company to run the supply chain in the most effective and efficient way. However, it comprises activities like logistics, production, sourcing, product development, and using information systems to develop connections among all of these activities.
Inventory Management
Inventory comprises work-in-process, supplies, finished goods, and unprocessed material. The Inventory management system manages the company’s inventory from storage to the point of sale. You have to create a balance between the actual rate of sale and inventory size items. Storage cost would increase the cost that you won’t be able to recover.
Service Design
Service design is when a company improves the quality of engagement between the customers and service providers by planning, organizing, material component, communication, and infrastructure. It’s a way to make changes in the existing product or develop a new product entirely.
Quality Control
Quality control is a part of management that focuses on meeting the quality requirement of the company. It addresses questions like production process, the product made, check and balance of quality control. We can say it’s the process of performing operational activities in order to meet the quality requirements.
Managing the Productivity
Productivity
Productivity is the comparative ratio of the company’s output to the input in the system. The system would be productive if the rate is higher.
Ways to improve productivity
There are many ways to improve productivity. You can do it by focusing on three elements;
- Job-related
- Resource related
- Environment-related
Conclusion: What is Operation Management? Roles & Planning Operation System
After an in-depth study of what is operation management, its various roles, and planning operation system; we’ve realized that operation plays a significant role in developing its product. If you want to learn about the operation system, then keep in mind the abovementioned various parts.
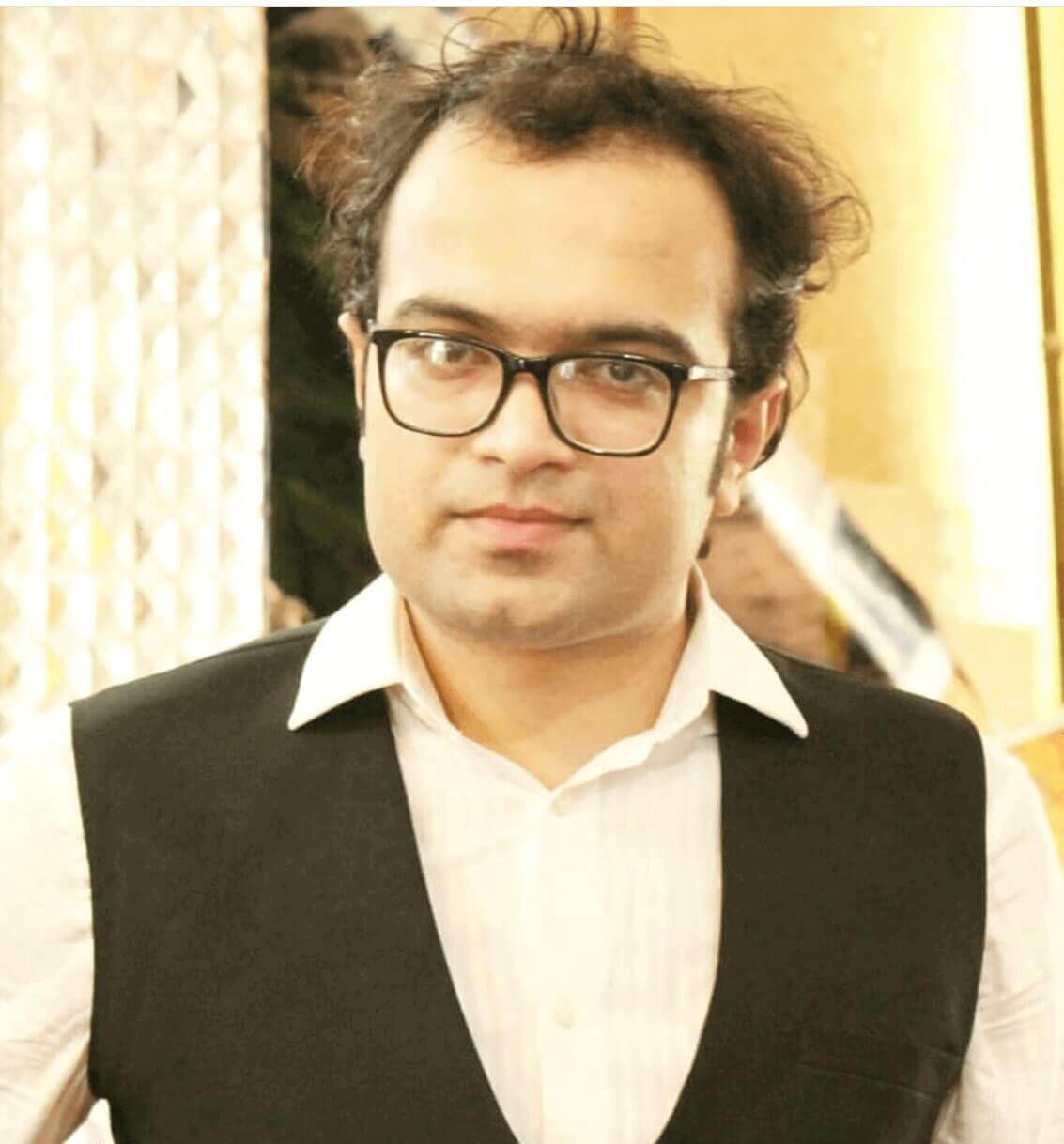
Ahsan Ali Shaw is an accomplished Business Writer, Analyst, and Public Speaker. Other than that, he’s a fun loving person.